Finned tubes(also known as Fin Tubes in technical terminology) are specialized heat-exchange components designed to amplify thermal efficiency by extending the surface area of base tubes through attached fins. This innovation transforms ordinary tubes into high-performance heat exchangers, making them indispensable across industries ranging from energy production to HVAC systems.
- Structure of Finned Tubes
- Base Tube: Typically constructed from corrosion-resistant materials like stainless steel, carbon steel, or copper-nickel alloys to withstand harsh environments.
- Fins: Attached via welding, extrusion, or mechanical bonding; common shapes include spiral fins, longitudinal fins, and serrated fins. These geometries increase surface area by 5–10x compared to smooth tubes. Common materials are stainless steel, carbon steel, aluminum, copper.
Type | Structure | Materials | Manufacturing Process | Thermal Efficiency | Examples |
Welded Finned Tubes | Fins attached to the base tubes via welding | CS SS | High-frequency welding(HFW) Medium frequency welding Laser welding | High (disrupts thermal boundary layers) | HFW Serrated Finned Tubes Longitudinal Finned Tubes H Type Finned Tubes Laser Welded Finned Tubes |
Embedded Finned Tubes | Fins mechanically bonded into grooves on the tube surface | Aluminum copper | Groove machining + fin insertion | Moderate (depends on bond quality) | G Type Embedded Finned Tube |
Extruded Finned Tubes | Fins formed by extruding the base tube material into fin shapes | Aluminum copper | Cold extrusion | High (seamless fin-tube bond) | Extruded Finned Tubes Integral Low Finned Tubes Integral High Finned Tubes |
Tension-Wound Finned Tube | Fins mechanically wrapped around a base tube | Aluminum copper | Tension-Wound | Moderate (depends on bond quality) | L, LL, KL-Foot Fin Type Finned Tubes |
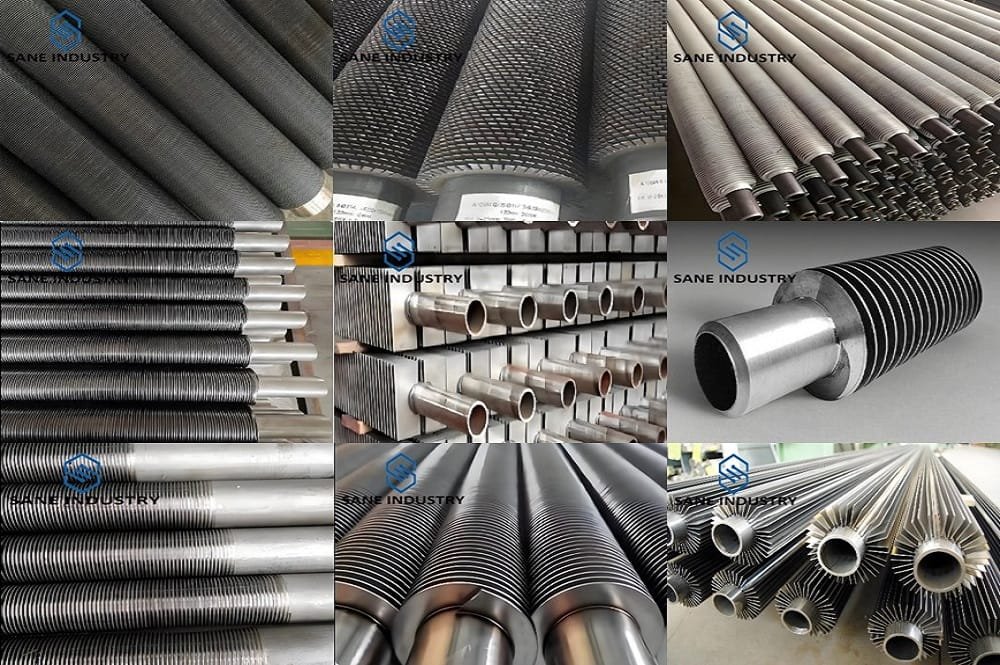
- Working Principle of Finned Tubes
Step 1: High-temperature fluid flows through the inner tube, transferring heat to the tube walls via conduction.
Step 2: Heat spreads across the fins, leveraging their extended surface area to amplify thermal diffusion.
Step 3: Ambient air/fluid absorbs heat from the fins through convection, cooling the system.
- The Use of Finned Tubes
- Industrial Heat Exchangers
Shell-and-Tube Heat Exchangers: Widely used in refineries and chemical plants for gas-liquid or liquid-liquid heat exchange, particularly in processes requiring corrosion resistance or high-temperature tolerance.
Waste Heat Recovery Systems: Integrated into boilers, furnaces, and kilns to capture and reuse exhaust heat, improving energy efficiency in industries like metallurgy and cement production.
- Air-Cooling Systems
Power Plant Cooling: Deployed in air-cooled condensers (ACCs) to replace water-cooled systems in arid regions, reducing water consumption while maintaining thermal performance.
Petrochemical Facilities: Utilized in air-cooled heat exchangers for condensing hydrocarbons or cooling process fluids, with elliptical finned tubes offering lower air-side resistance compared to circular designs.
- Chemical and Refining Processes
Cracking Furnaces: Applied in ethylene production to enhance heat transfer efficiency between combustion gases and reactor tubes.
Desulfurization Units: T-type finned tubes improve reboiler performance in sulfur recovery systems by increasing turbulence and heat transfer rates.
- HVAC and Refrigeration
Condensers/Evaporators: Optimize heat exchange between refrigerants and air in commercial HVAC systems, reducing energy consumption.
Radiators: Aluminum-finned tubes are common in automotive radiators for engine cooling due to their lightweight and high thermal conductivity.
- Emerging Applications
Elliptical Finned Tubes: Gaining traction in European industries for air-cooled exchangers, offering superior aerodynamic performance over traditional circular tubes.
Advanced Fin Designs: H-type and closed finned tubes are adopted for specialized applications requiring ultra-high heat transfer coefficients or reduced fouling.
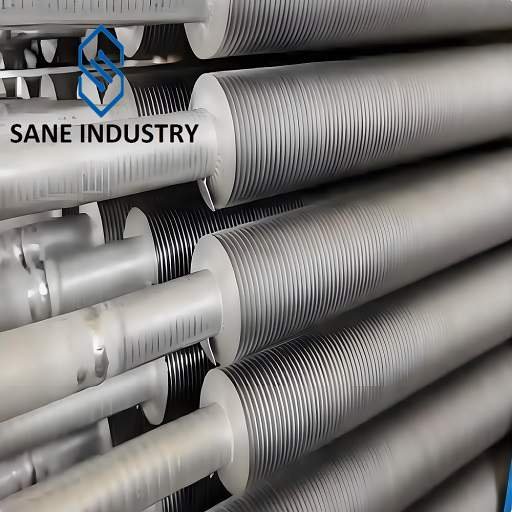
- Advantages & Disadvantages of Finned Tubes
Advantages
- Enhanced Heat Transfer Efficiency
The finned structure significantly expands surface area, enabling rapid heat exchange and superior thermal conductivity.
High thermal performance allows efficient heat dissipation even in low-temperature conditions.
- Compact and Space-Saving Design
Occupies minimal space compared to traditional heat exchangers, ideal for confined industrial or workshop environments.
- Corrosion and Pressure Resistance
Aluminum or steel-based variants exhibit excellent corrosion resistance, ensuring durability in humid or chemically aggressive environments.
Robust construction supports high-pressure applications.
- Versatility and Adaptability
Compatible with diverse media (liquids, gases) and operational conditions (high temperature/pressure).
Suitable for combined use with other heat exchange components to optimize system performance.
- Low Maintenance and Easy Installation
Lightweight materials and modular designs simplify installation and relocation.
Detachable fins facilitate cleaning and maintenance without disassembling the entire system.
Disadvantages
- High Manufacturing and Maintenance Costs
Complex finned structures and precision machining increase production costs.
Regular cleaning and anti-corrosion treatments are required to maintain efficiency, adding to operational expenses.
- Environmental Sensitivity
Dust accumulation on fins reduces heat transfer efficiency, necessitating frequent cleaning in polluted environments.
Performance may degrade under extreme flow velocities or poor air circulation.
- Noise Generation
High-speed airflow through fins can generate noticeable noise during operation, impacting user comfort.
- Material Limitations
Aluminum fins, while lightweight, may lack the mechanical strength of steel in high-stress scenarios.
In conclusion, finned tubes, with their 3–10x enhanced thermal efficiency through expanded surface area, offer versatile solutions across industries. By integrating corrosion-resistant materials and adaptive geometries, they balance compactness and durability in applications like refinery heat exchangers and HVAC systems. With continuous innovations in fin design and material engineering, they remain pivotal for sustainable, energy-efficient thermal management worldwide.
If you have any questions or inquires for finned tubes, please feel free to contact with Allen@sanesteel.com. You are sure to get the best and most cost-effective solution.